Winterize, Service and Inspect your trucks, including any spares
- Make sure EnergyTrack is fully operational (handhelds charged daily, printers functional, totalizers import properly)
- Keep extra rolls of printer paper in the cab of each truck
Last Delivery Date Report
Report Menu – Tank Reports #3 Last Delivery Date Report
- Helps determine which auto-fill customers have not had a delivery since last season
- Run from January 1st through April 30th for all delivery type 2 tanks
- If a customer is on this list, they did not receive a summer or fall fill and are at risk for a run-out
- Enables being pro-active with contacting the customer before a run-out occurs and helps to determine why a customer has not been delivered to as planned
Excel Export Version
Review the Call-In Entry Screen
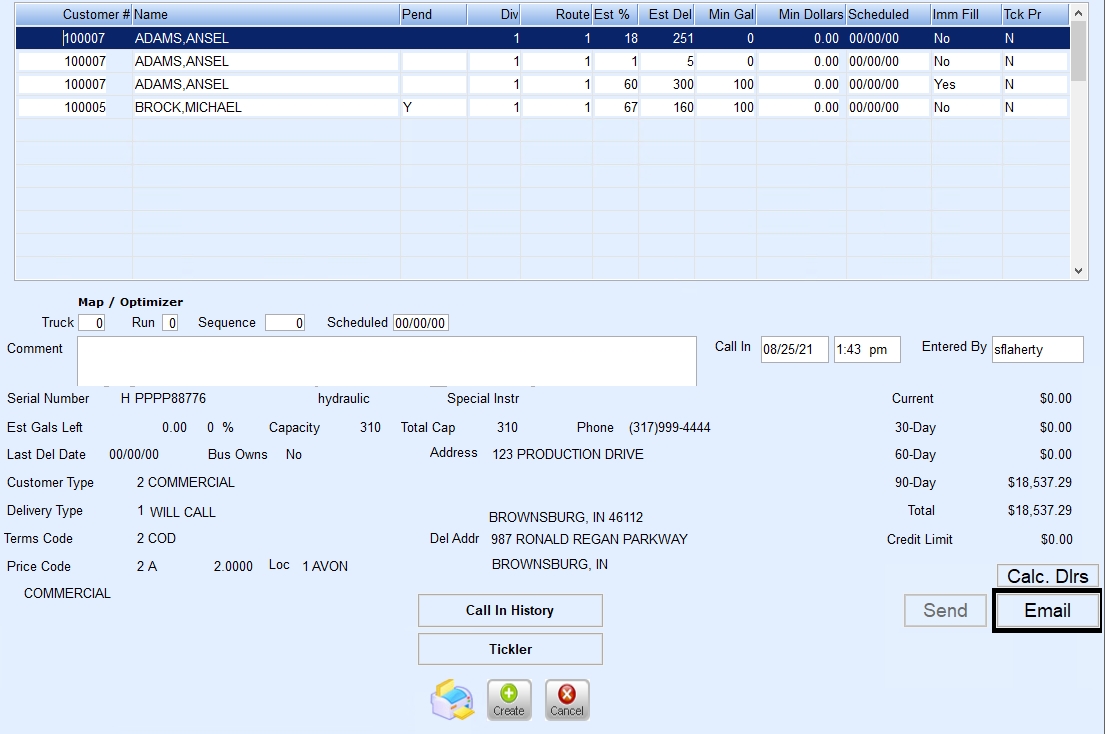
- Now is the perfect time to evaluate the Call-In entry program to assess upcoming, pending, or past due deliveries
- For example, how many call-ins are more than one month old?
- Highlight, Ctrl+M, and press F3 to remove past due deliveries after investigating
- Every call-in request must be entered in this screen for the OptimzerPlus system to route
- Scheduled Dates and Immediate Fills should be kept to a minimum. Otherwise, these deliveries drive the route for the day
Remote Tank Monitors
Monitors will lessen demand on working K-Factors and Daily Usage
- Gallons/Percent Update must be selected on Meter/Monitor screen
- Target and Critical Refill Levels must have a 10% difference
- OptimizerPlus+ routes the tank based on individualized settings per RTM
- Critical set points to consider for high demand tanks:
- If tank consumes through 30% of its storage within 3 days, set to 30% or 40%, especially if in a remote area
- If possible, need to upsize storage
- Should be read daily
- Slow consumption customers are routed closer to the lower limit threshold if conditions merit:
- Drive by daily
- Slow steady usage
- In an area with concentrated tanks, and ETC
Review Route Stat Emails
Check daily route stat emails
- Are you over-capacity?
- Run additional trucks if necessary
- Do you have repeating tanks? WHY??
- Run OptimizerPlus+ Compliancy reports to determine if tanks are being skipped
- Parked Trucks? – Is there an error or does the Opti-Tool need adjusted?
Other Items to Review
Listen to the drivers!!
They’re your first line of defense. If something’s wrong, or if something changes, it’s important to listen and review.
- Drivers are the most important in educating customers to call in at 20%. The customers will help out the drivers. All employees need to stress 20%
- Know which tanks to set up for Auto-Schedule or Will-Call
- Wood Burners – Customer must participate in tracking their tanks
- Heat Pumps – Best handled by monitor
- Heat tanks with swimming pool – Best handled by monitor
- Seasonal (lake homes, cabins) – Best handled by monitor or Julian
- This customer is your greatest liability risk
- Shop/Garage – Inconsistent usage. Best handled by monitor or Will-Call
- Delivery Types
- Once a year fill tanks:
- Set up with Customer Type (SummerFill/ Will-Call Winter)/ Delivery Type (Will-Call)
- In Matrix set Optigistics Tank Type as C for winter and SummerFill Tanks Type as S
- This will route summer fills more efficiently
- If customer needs propane in winter, they will need to call
- This will need to be communicated with customers
- Set up with Customer Type (SummerFill/ Will-Call Winter)/ Delivery Type (Will-Call)
- Once a year fill tanks:
- Make sure drivers communicate by the end of each day to prevent duplicate routes
- Review Tanks Not Plotted report daily found at Customer Menu/Tanks Not Plotted
- Review HH GPS Changes > .25 Miles exception report
- Review K-Factor deviation reports and adjust K-Factors as necessary
- Ticklers – Make certain driver comments have been reviewed and addressed
- Additional Items for Success
- Do NOT attempt to play with settings during peak delivery season!
- If changes are made to trucks, drivers, or route settings, always perform a test run of the OptimizerPlus+ to ensure routes will process without error
OptimizerPlus+ Driver Maintenance
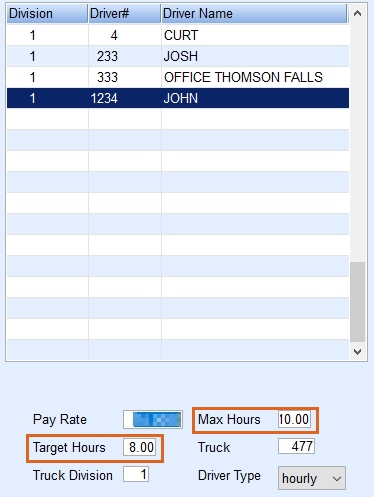
- Make sure driver hours are accurate for the heating season
- Target Hours – The minimum number of hours the OptimizerPlus+ should schedule each day
- Max Hours – The maximum number of hours for the OptimizerPlus+ to consider for delivery each day (maximum hours are only used if necessary for over-capacity)
- Target and Max Hours are customizable per driver but should have a 2 hour spread between Target and Max Hours
OptimizerPlus+ Calendar Tool
Exclusions
Bad weather pending or a driver on vacation? Make sure to set up Exclusion dates to push projected critical deliveries to an earlier date.
- Helps prevent run outs and over-capacity issues during the time period
- Can be applied to specific routes or all routes
- Automatically turns on and off by itself
- Can also be set annually for holidays such as Christmas or New Year’s Day
- Excluded date(s) will not have a route unless there is a critical tank still pending or an unexpected critical is scheduled (call-in, Julian)
- In this example, Friday, December 6th, has been excluded for route 1
- The delivery window has been set to push forward critical deliveries to Dec 2nd through Dec 5th
- The driver hours have been extended from 8 hours to 10 hours per day
- Route Stats will display the exclusionary delivery period as an E
- The day of exclusion displays as an E+ and the route will be parked
Override Parked Trucks
Not comfortable with parked trucks in the winter?
- You can set the OptimizerPlus+ Calendar Submodes tab to Override Parked Trucks based on minimum delivery criteria
- If a route cannot meet the minimum criteria, it will not generate a route
- You can override parked trucks for all routes, or specific routes
- Standardize if possible, for all your routes!
- Enter Division & Route and press Add button
- Select Override Parked Trucks When in the Mode Flag section
- Enter variables to determine when to over-ride a parked truck
- The example above shows to override if the truck will pump at least 1000 gallons with a minimum of 20 mpg and at least 3 stops
- Select Update (Add button turns to Update when pressed)
Mode Flags
Set Mode Flags to tell OptimizerPlus+ how to handle Over-Capacity situations
- Fill Most Critical Tanks First (recommended) – The OptimizerPlus+ will schedule critical tanks based on current levels of the tanks and estimated days until empty. Tanks with lower capacity are given priority
- Fill Largest Number of Critical Tanks – OptimizerPlus+ will prefer to schedule as many critical tanks as possible regardless of estimated days till empty
- Fill Critical Tanks Immediately – The OptimizerPlus+ will attempt to schedule all critical tanks on the first day, meaning all tanks will be given the same priority
- Fill Critical Tanks Within 2 Days – For large routes, the OptimizerPlus+ will delay scheduling a critical tank until the next day only if the tank’s remaining propane allows for it. Tanks estimated to run out on the 1st day is given priority
Ultimate Rule for Success?
Above all else, make sure to drive the route as scheduled!